Alright, let me tell you about this little project I tackled recently. It was basically down to choosing between two ways of doing something, which I ended up just calling the ‘higgins’ method and the ‘addison’ method in my notes. Don’t ask me why those names, they just stuck.
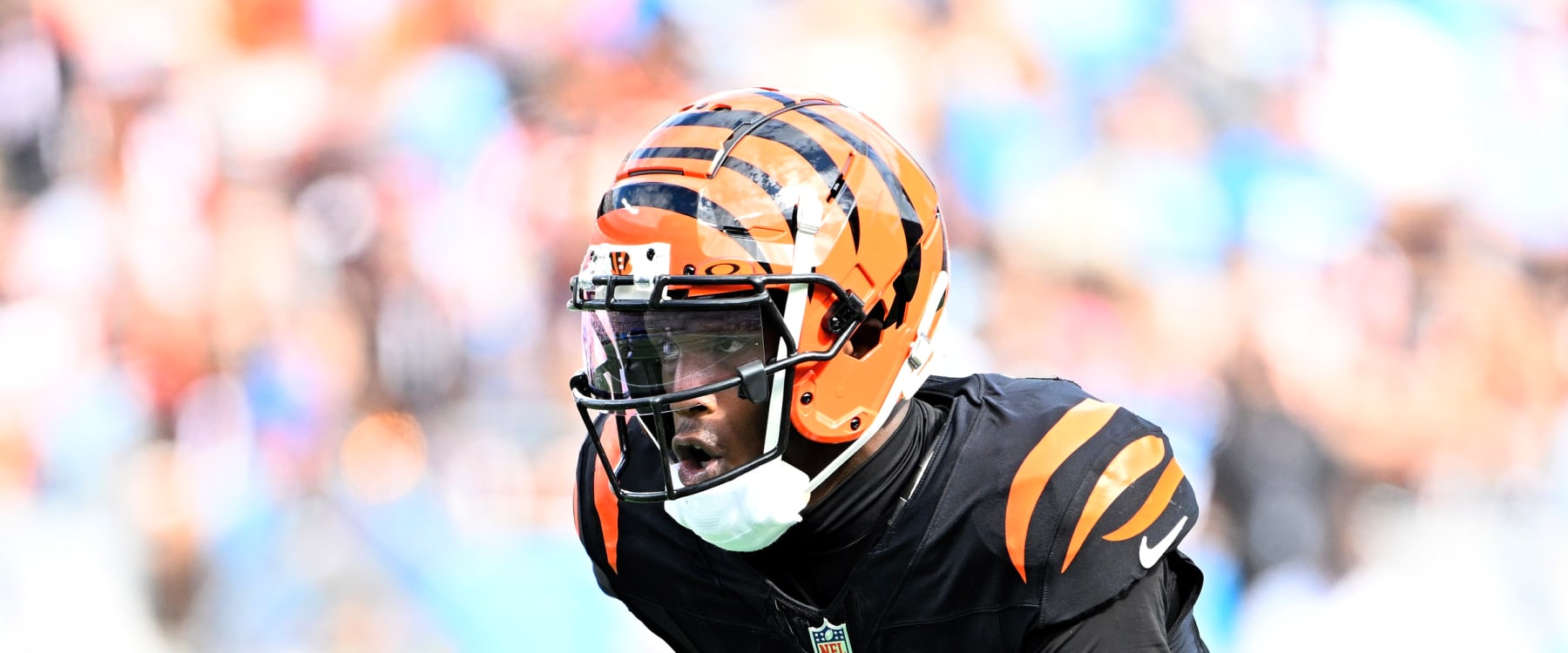
Setting the Stage
So, the whole thing started because my workshop space, specifically where I keep all my small components – resistors, capacitors, tiny screws, you know the drill – was an absolute disaster zone. I’d just been tossing things into vaguely labelled bins for ages, and finding anything specific was turning into a real treasure hunt, emphasis on the ‘hunt’. Wasted so much time just rummaging.
I knew I needed a system. A proper one. I started looking around, reading bits here and there online, talking to a buddy who’s way more organized than me. That’s where these two main ideas came from.
Trying out ‘Higgins’
First up, I decided to give the ‘higgins’ approach a go. This seemed like the more common way, I guess. The idea was basically to sort everything by type first, then by value or size.
- I got a bunch of small drawer cabinets.
- I designated drawers for resistors, others for capacitors, others for ICs, etc.
- Within the resistor drawers, I started sorting them by their resistance value using smaller dividers. Same logic for capacitors (value and voltage) and other stuff.
It took a solid afternoon. Felt productive, you know? Everything looked neat. But then, when I actually started working on a project the next day, I found myself constantly pulling out multiple drawers. Need a specific resistor? Open the resistor drawer. Need a specific capacitor? Open the capacitor drawer. Need a transistor? Open another drawer. It was organised, yes, but still felt kinda inefficient for actual project workflow.
Switching to ‘Addison’
I lived with ‘higgins’ for about a week, but the drawer-hopping got old fast. That’s when I decided to tear it down and try the ‘addison’ method. This one was a bit different, more project-centric, or maybe kit-centric is a better word.
The core idea here was to group components commonly used together.
- I got some different organisers, specifically small tackle-box style ones with configurable compartments.
- Instead of ‘all resistors here’, I started making kits. For example, one box became my ‘Arduino Basics Kit’ with common resistors, LEDs, jumper wires, a few basic sensors, the capacitors I always use with them, etc.
- Another box became my ‘Power Supply Kit’ with different regulators, input/output caps, diodes, terminals.
- Another was for ‘Audio Stuff’ – op-amps, jacks, specific caps and resistors I use for filters.
This felt… weird at first. Like I was breaking some sacred rule of component organization. Duplication became a thing – I had 10k resistors in multiple boxes! But I pushed through.
The Result and My Take
Setting up ‘addison’ also took time, maybe even a bit more thought because I had to anticipate what I’d need for typical project types. But man, when I started my next build? It was so much smoother.
Starting an Arduino project? Grab the ‘Arduino Basics’ box. Need to build a power circuit? Grab the ‘Power Supply’ box. Most of what I needed was right there in one or two boxes. Less jumping around, more building.
So, for me, ‘addison’ won. It’s not perfect. Sometimes I still need a specific weird component from a ‘general stock’ backup box. And yes, there’s duplication. But the time saved during actual project work outweighs the setup hassle and the cost of a few extra common components.
Ultimately, the ‘higgins’ method (type/value sorting) looks super tidy and is probably great if you’re just managing inventory or need to find one specific part value across your entire stock. But for my hands-on, project-based workflow, the ‘addison’ method (kitting/grouping by function) just makes more practical sense. It reduced the friction of actually doing the work. Just my two cents from spending a weekend wrangling tiny bits of plastic and metal.